

Otherwise, the Types 302, 304, 304L and 305 alloys may be considered to perform equally in most corrosive environments. The data for formic acid, sulfuric acid and sodium hydroxide illustrate this. In some cases, the low carbon Type 304L alloy may show a lower corrosion rate than the higher carbon Type 304 alloy. Boiling 50 percent caustic is likewise too aggressive. The more highly reducing environments such as boiling dilute hydrochloric and sulfuric acids are shown to be too aggressive for these materials. The 9 to 11 percent of nickel contained by these 18-8 alloys assists in providing resistance to moderately reducing environments. These alloys are also resistant to moderately aggressive organic acids such as acetic, and reducing acids such as phosphoric. The 18 to 19 percent of chromium which these alloys contain provides resistance to oxidizing environments such as dilute nitric acid. In addition, a large variety of applications involve household and industrial chemicals. Building facades and other architectural and structural applications exposed to non-marine atmospheres also heavily utilize the 18-8 alloys. Heat exchangers, piping, tanks and other process equipment in contact with fresh water also utilize these alloys. The alloys are used widely in equipment and utensils for processing and handling of food, beverages and dairy products. The Types 302, 304, 304L and 305 austenitic stainless steels provide useful resistance to corrosion on a wide range of moderately oxidizing to moderately reducing environments. Type 305 is used for applications requiring a low rate of work hardening during severe cold forming operations such as deep drawing. Type 304L is used for welded products which might be exposed to conditions which could cause intergranular corrosion in service.

There are instances, such as in temper rolled products, when Type 302 is preferred over Type 304since the higher carbon permits meeting of yield and tensile strength requirements while maintaining a higher level of ductility (elongation) versus that of the lower carbon Type 304. Past users of Type 302 are generally now using Type 304 since AOD technology has made lower carbon levels more easily attainable and economical. Food and beverage, sanitary, cryogenic, and pressure-containing applications are examples. These alloys are covered by a variety of construction or use of equipment manufactured from these alloys for specific conditions.
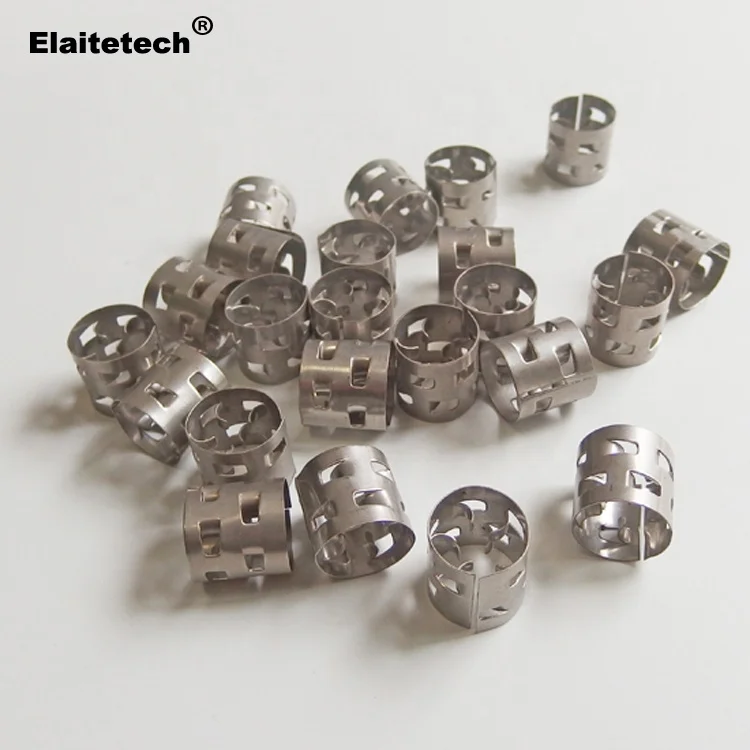
Types 302 and 305 are used in smaller quantities. Type 304 represents the largest volume followed by Type 304L. This combination of properties is the reason for the extensive use of these alloys which represent nearly one half of the total U.S. Ready availability of a wide range of product formsĮach alloy represents an excellent combination of corrosion resistance and fabricability.Good strength and toughness at cryogenic temperatures.These alloys may be considered for a wide variety of applications where one or more of the following properties are important:

Types 302, 304, 304L, and 305 stainless steels are variations of the 18 percent chromium – 8 percent nickel austenitic alloy, the most familiar and most frequently used alloy in the stainless steel family.
